Leading AI manufacturing tools include Uptake and SparkCognition for predictive maintenance, Landing AI and Instrumental for quality control, and ABB and Boston Dynamics for robotics. Siemens’ Tecnomatix and Autodesk’s Fusion 360 handle process design, while Coupa’s LLamasoft optimizes supply chains. These tools reduce downtime by 30% and cut costs up to 61%. The AI manufacturing market’s growth to $8.57 billion by 2025 signals major advances in smart automation ahead.
Key Takeaways
- LandingLens and Instrumental lead in AI-powered defect detection and quality control systems for manufacturing processes.
- SparkCognition and Uptake offer advanced predictive maintenance solutions using multiple data science models to prevent equipment failures.
- Siemens Tecnomatix and Autodesk Fusion 360 provide comprehensive AI-driven design and manufacturing process optimization tools.
- ABB and Boston Dynamics deliver specialized robotics solutions, from fixed-position industrial robots to mobile units for complex environments.
- Coupa’s LLamasoft implements digital twin modeling and AI analytics for optimizing manufacturing supply chains and inventory management.
Why AI Tools Are Revolutionizing Manufacturing
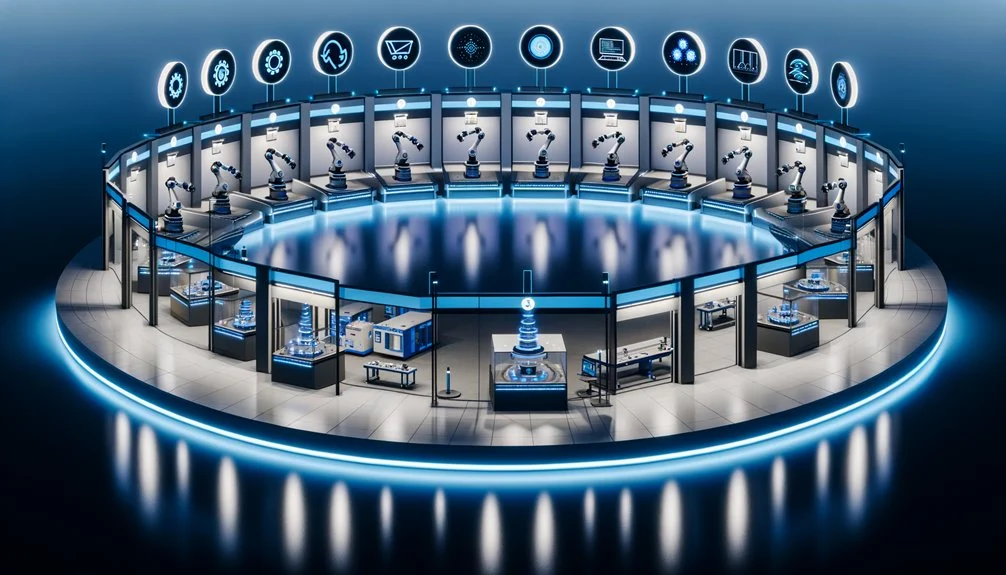
As manufacturing evolves in the digital age, AI tools are transforming how products are made, designed, and delivered. These tools are making factories smarter, faster, and more efficient than ever before. The impact is clear: AI is expected to be used in over 60% of new product introductions by 2025.
AI’s revolution in manufacturing comes from its ability to handle multiple tasks. It spots defects in products, predicts when machines need maintenance, and manages inventory levels automatically. Smart robots work alongside humans, while virtual prototypes help test new designs without expensive physical models. AI even creates digital twins of entire manufacturing systems for real-time monitoring. Companies are increasingly making AI a strategic priority, with 83% of businesses now considering AI implementation essential to their manufacturing plans. AI-powered quality control systems achieve 90% accuracy in defect detection, significantly reducing production errors. With computing infrastructure advancements, manufacturers can now process vast amounts of data in real-time for better decision-making.
AI transforms manufacturing by automating tasks, from quality control to maintenance, while enabling advanced simulations and real-time system monitoring.
The numbers show AI’s growing importance. The AI manufacturing market will reach $8.57 billion by 2025, and 78% of businesses already use AI in their processes.
With private investment in generative AI reaching $33.9 billion globally, the manufacturing revolution is well underway.
Predictive Maintenance With Uptake and Sparkcognition
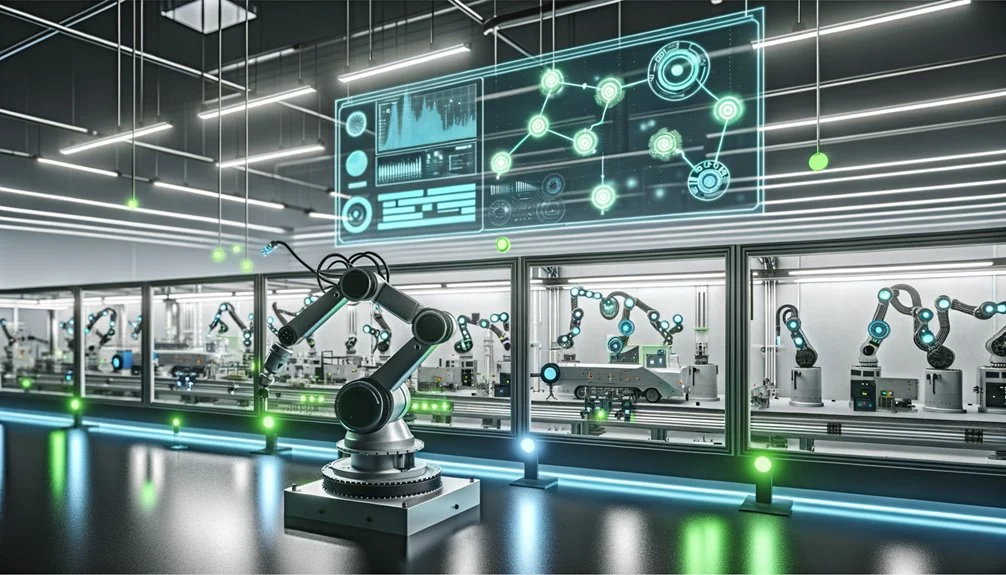
Two leading companies, Uptake and SparkCognition, are revolutionizing predictive maintenance in manufacturing through advanced AI solutions.
Uptake partners with Daimler Truck North America, using over 65 data-science models to predict component failures and reduce repair costs. Their SaaS platform offers real-time intelligence about vehicle parts and subsystems. Real-time monitoring through IoT devices enables continuous data collection for more accurate predictions.
SparkCognition collaborates with major companies like Boeing and Verizon, using AI and machine learning to analyze sensor data. Their SparkPredict platform monitors machines in real-time and identifies potential equipment failures before they happen.
Both companies are making significant impacts in manufacturing. The integration of sensor intelligence analytics provides actionable insights that enhance decision-making capabilities for maintenance teams. They help extend asset lifespan through early problem detection and optimize maintenance schedules.
Uptake has earned recognition from Gartner and the World Economic Forum, while holding over 45 patents. Their combined technologies are reducing unplanned downtime and improving operational efficiency across various industries.
Quality Control Excellence Through Landing AI and Instrumental
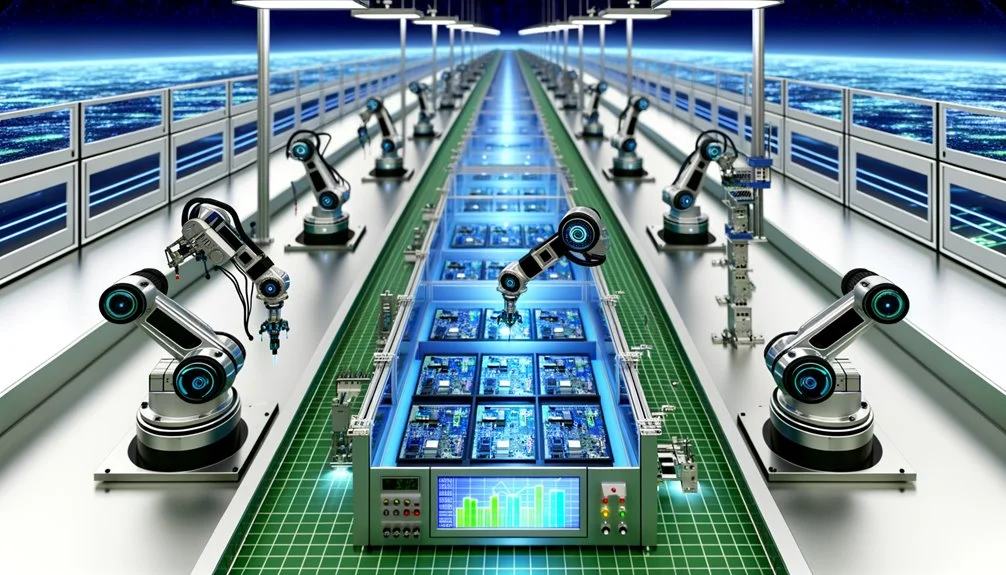
While manufacturers have long relied on human inspectors for quality control, Landing AI and Instrumental are transforming this process through advanced computer vision and artificial intelligence.
Both platforms use sophisticated AI algorithms to detect product defects faster and more accurately than traditional methods. Landing AI’s LandingLens platform enables companies to create and deploy custom inspection models, while Instrumental focuses on automated defect detection and root cause analysis. The evolution of these systems marks a significant upgrade from traditional machine vision approaches of the late 20th century. Their ability to detect soldering defects helps ensure consistent product quality across manufacturing lines. The platforms leverage data visualization tools to present quality metrics clearly to stakeholders.
- Landing AI excels in multiple industries including electronics, textiles, and assembly, helping catch defects early in production.
- Instrumental’s real-time alerts and data analytics help manufacturing engineers quickly solve quality issues.
- Both systems reduce human error and fatigue-related mistakes in the inspection process.
- The platforms integrate with existing production line cameras and software, making implementation straightforward.
These AI-powered solutions are making quality control more efficient and reliable while providing valuable data for continuous improvement.
Smart Robotics: ABB and Boston Dynamics Leading the Way
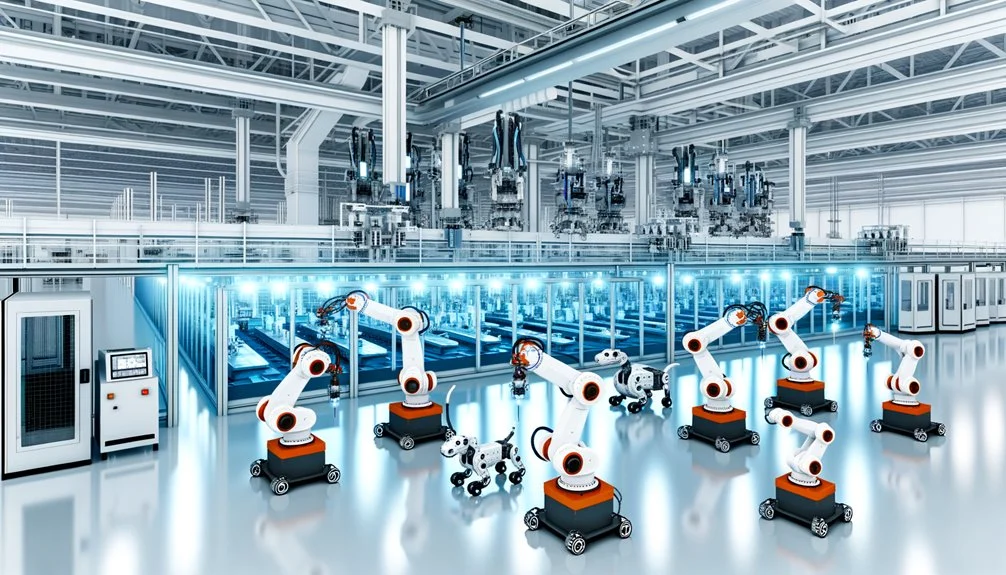
Leading the industrial robotics revolution, ABB and Boston Dynamics represent different but complementary approaches to manufacturing automation.
ABB specializes in fixed-position industrial robots with six-axis arms that excel at precise, repetitive tasks in structured environments. With over 400,000 installations worldwide, ABB’s robots are the backbone of many manufacturing facilities, performing tasks like welding and assembly. Their delta spider robots can achieve remarkable speeds of up to 120 picks per minute. The company maintains a strong can-do energy in developing automation solutions across multiple industries.
Fixed-position industrial robots from ABB dominate global manufacturing, with precision arms performing critical assembly and welding operations worldwide.
Boston Dynamics takes a different path, focusing on mobile robots that can navigate complex terrains. Their Spot robot walks on four legs to perform industrial inspections, while their Stretch robot handles boxes in warehouses. These robots use advanced sensors and AI to move and work autonomously. The implementation of modular design principles allows their robots to function independently in various scenarios.
Both companies bring unique strengths to manufacturing. ABB’s robots deliver reliability and precision in controlled settings, while Boston Dynamics’ machines adapt to changing environments.
Together, they’re pushing the boundaries of what’s possible in modern manufacturing automation.
Supply Chain Optimization Using Llamasoft and ClearMetal
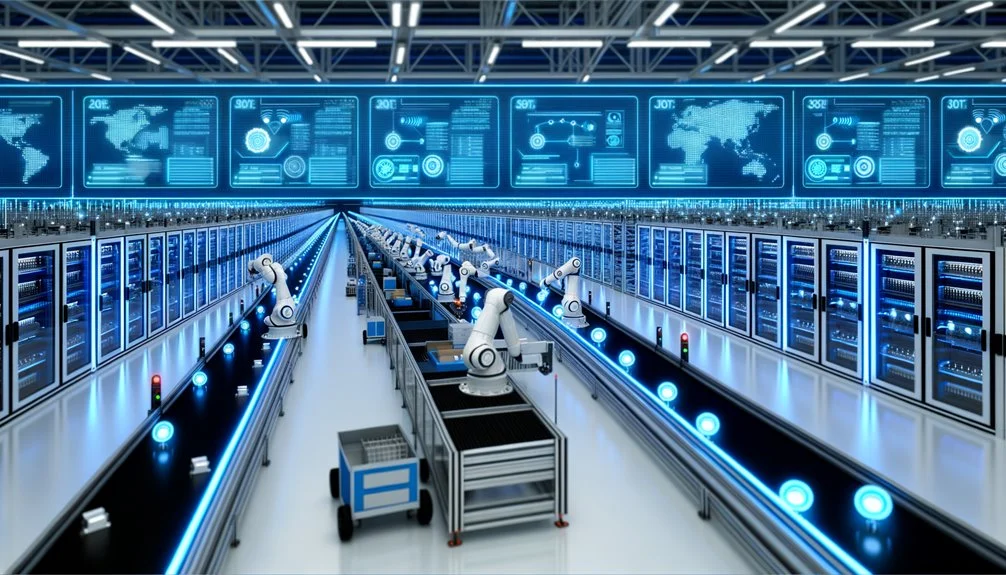
Modern supply chain management has been revolutionized by Coupa’s LLamasoft platform, which uses digital twin modeling and AI-driven analytics to optimize complex business operations. The system helps companies make better decisions about production, inventory, and transportation by creating virtual models of their supply chains. The platform enables trusted AI algorithms to guide strategic planning and decision-making processes.
Network optimization algorithms find the best ways to structure operations, while production planning tools facilitate efficient manufacturing processes. The platform’s comprehensive process step mapping ensures complete visibility into production workflows. Companies can test different scenarios without risk and quickly adapt to changing market conditions.
- Digital twin technology creates unlimited simulations to improve revenue and reduce carbon emissions
- AI-powered planning tools speed up decision-making across teams
- Network optimization finds ideal routes and capacity allocation to meet customer demand
- Advanced forecasting helps companies maintain proper inventory levels and respond to disruptions
The platform’s visualization tools make it easy to spot problems and inefficiencies, while its risk management features help prevent supply chain disruptions.
Process Design Innovation With Siemens and Autodesk
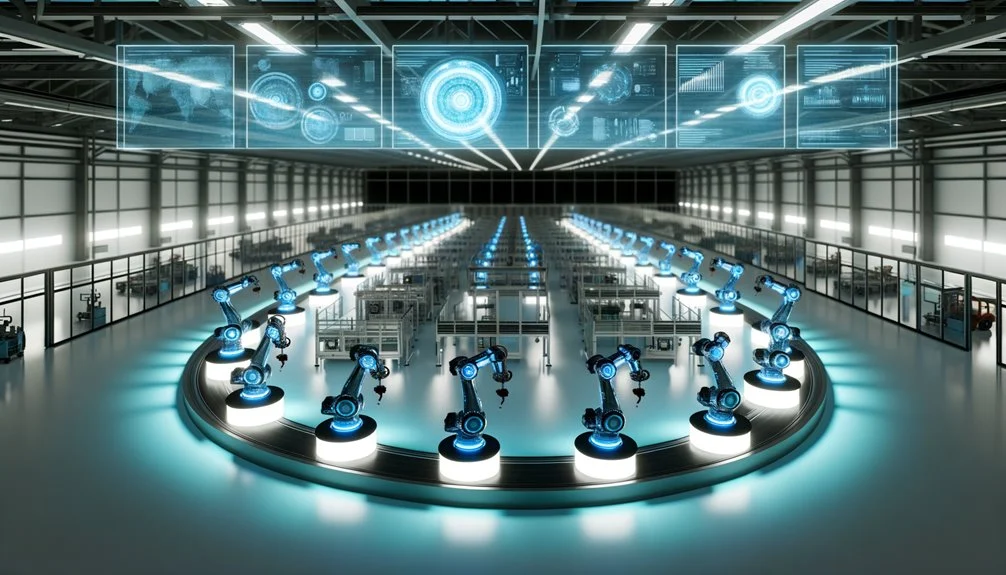
Today’s manufacturing processes benefit from advanced software tools created by industry leaders Siemens and Autodesk.
These companies offer solutions that make factories smarter and more efficient. Siemens’ Tecnomatix and Teamcenter platforms help plan manufacturing operations by creating detailed blueprints of what to make and how to make it.
Their NX software combines different manufacturing tasks like 3D printing and robotic control in one place. The company’s cloud-based tools help teams work together while reducing production time. Siemens’ Insights Hub capabilities provide actionable data for optimizing smart manufacturing operations. Process manufacturing software enables batch tracking to maintain precise quality control during production.
Autodesk brings its own innovations through Fusion 360, which combines design and manufacturing in a single platform.
Their PowerMill software makes CNC machining more precise and efficient. Both companies’ tools use cloud technology to help teams collaborate in real-time.
These digital solutions create connected manufacturing environments where designers, engineers, and production teams can work together seamlessly while improving factory performance and reducing mistakes.
Real-Time Analytics Platforms Transforming Production
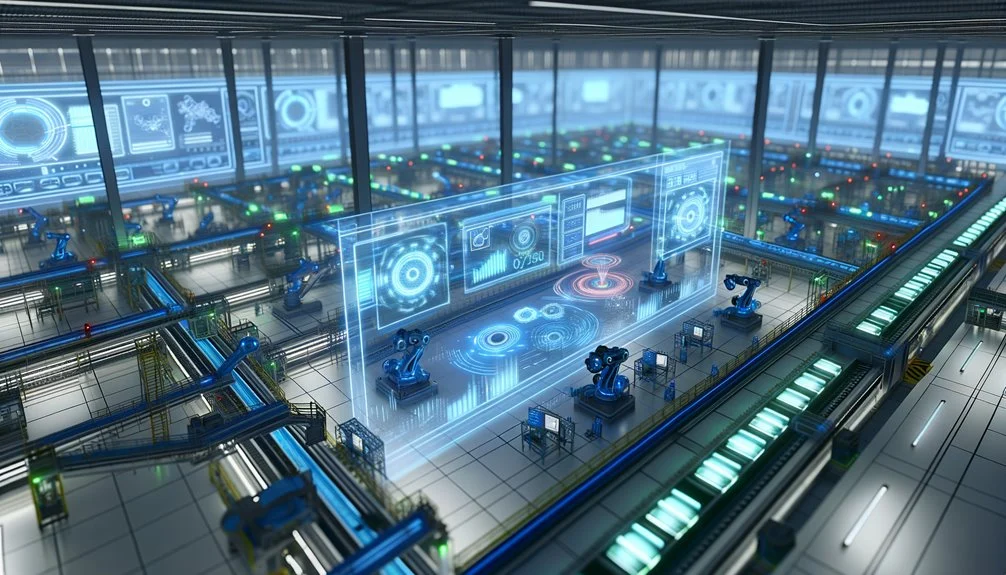
As manufacturing facilities seek greater efficiency, real-time analytics platforms have become essential tools for transforming production processes. These platforms connect multiple data sources, including machines, quality systems, and enterprise software, to create a complete view of operations. They process information instantly, helping factories detect issues and make quick decisions based on current data. Manufacturers typically see a 20% efficiency increase when implementing these solutions.
- Integration capabilities allow factories to combine data from different systems, making it easier to monitor production across multiple locations.
- Real-time KPI monitoring shows important metrics like equipment effectiveness and downtime through easy-to-understand dashboards.
- Advanced analytics convert raw machine data into useful information that helps predict equipment failures.
- Automated data collection speeds up information sharing between teams and reduces manual recording errors.
The technology enables factories to spot problems early, reduce waste, and improve overall productivity through data-driven decision making. Modern platforms like ThoughtSpot offer AI-powered search capabilities that make it easier for teams to find and analyze manufacturing data quickly.
Cost Savings and Efficiency Gains From AI Manufacturing Tools
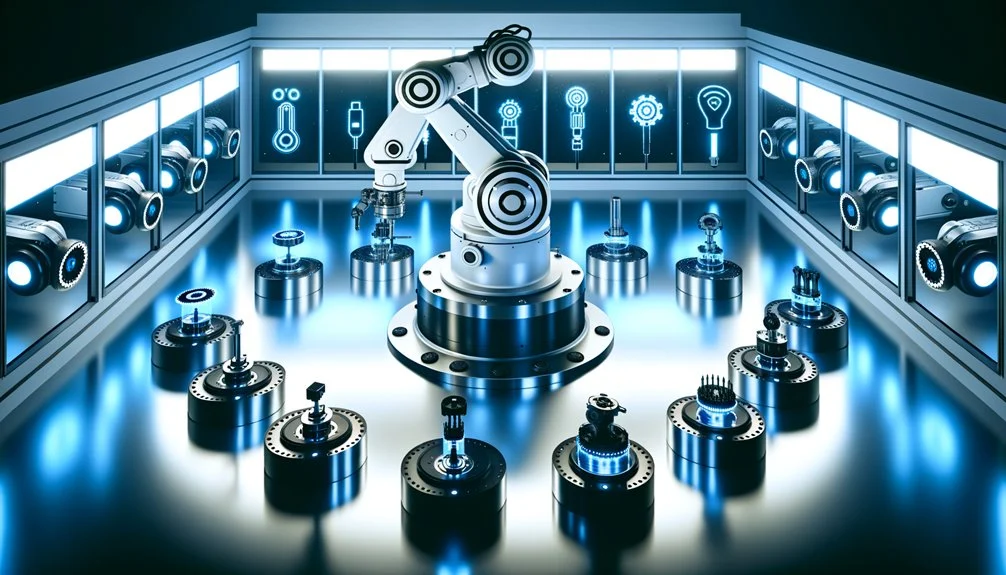
Manufacturing companies are discovering significant financial benefits through AI implementation. Studies show that 66% of manufacturers report major cost savings from using AI tools in their operations.
AI-powered predictive maintenance reduces equipment downtime by up to 30%. This means machines stay running longer and break down less often. Continuous monitoring by AI systems allows for 24/7 operation without productivity loss.
Supply chain planning with AI cuts costs by up to 61% through better inventory management and network optimization.
Companies like GM are using AI to analyze production data, which helps reduce material waste. AI quality control systems catch defects in real-time, leading to less waste and better products.
Energy costs go down when AI analytics optimize power consumption across factory operations.
Service operations costs have decreased for 54% of organizations using AI. Automated customer support, predictive demand forecasting, and robotic process automation help companies save money while improving efficiency.
According to global research, manufacturing businesses adopting AI technology achieve cost decreases over 20% in several key operational areas.
Selecting the Right AI Manufacturing Tools
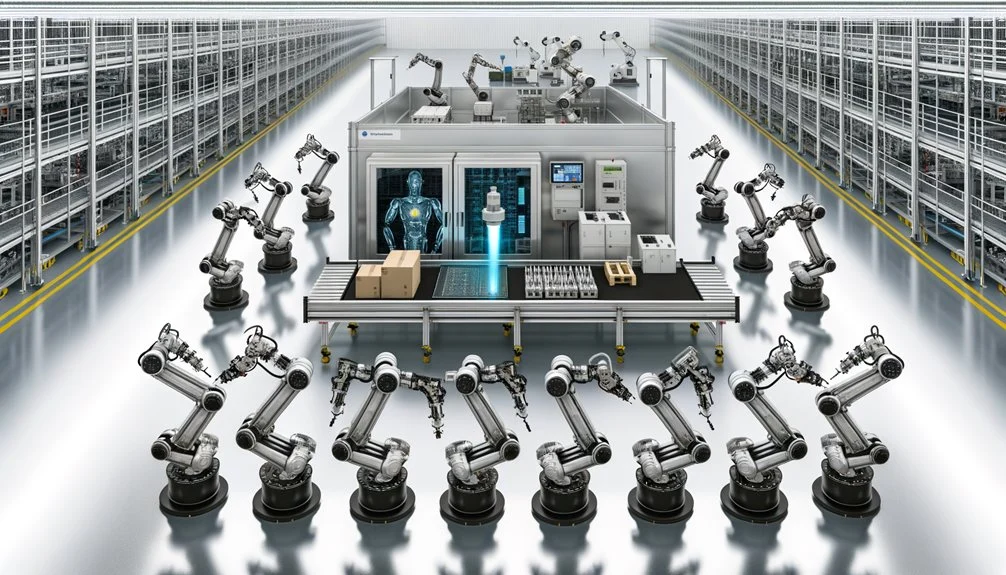
The selection of appropriate AI manufacturing tools requires careful consideration of multiple factors to assure successful implementation. Organizations need to evaluate vendor capabilities, technological fit, data security measures, and proven industry experience. A systematic approach helps match AI solutions with specific manufacturing needs and operational goals. The process includes team alignment meetings to ensure cohesive understanding of AI implementation benefits.
Recent studies indicate that with 69% of companies viewing AI as essential for their operations within three years, manufacturers must carefully evaluate their AI investment strategies. Organizations conduct self-assessments to define selection criteria based on business objectives, manufacturing processes, and operational challenges.
Vendors undergo evaluation for their AI capabilities, including machine learning algorithms, computer vision systems, and predictive analytics tools. Classification algorithms enable automated quality control by sorting manufactured items into defective and non-defective categories.
Data security and regulatory compliance verification assures protection of sensitive manufacturing information through encryption and access controls.
Continuous assessment frameworks track key performance indicators like defect rates, throughput improvements, and safety metrics.
This structured selection process enables manufacturers to identify AI solutions that align with their requirements while maintaining data security and operational efficiency standards.
Future Trends in AI-Powered Manufacturing Tools

Future innovations in AI-powered manufacturing tools point toward increasingly intelligent and autonomous systems.
These tools will leverage advanced IoT devices and edge computing to process data closer to the source, enabling faster decision-making on factory floors.
Enterprise IoT is expected to dominate the market, accounting for 72% of revenue by 2028.
This growth will drive smart automation and enhance data collection across manufacturing processes.
The integration of Industry 4.0 and 5.0 technologies will create more autonomous processes while maintaining human-machine collaboration.
Hyperautomation will enable quick, dynamic responses to production challenges, while unified platforms will better connect operational and information technology systems.
Data analytics are transforming manufacturing by identifying patterns and opportunities for process improvements.
These developments will support sustainability goals by optimizing energy usage and reducing waste.
Predictive maintenance capabilities will continue to evolve, using AI to forecast equipment failures and prevent costly downtime, while improving overall manufacturing efficiency.
Collaborative robots are being designed to work safely alongside human workers, creating a more productive and flexible manufacturing environment.
Conclusion
While AI manufacturing tools are transforming factory operations through automation and data insights, some worry about job displacement. However, studies show these tools actually create new roles for workers to manage and maintain AI systems. The technology continues to evolve rapidly, with improvements in machine learning algorithms and sensor capabilities pointing to even more advances in smart manufacturing in the coming years.